Fit for Service
Rama Challa, Matrix PDM Engineering, USA presents a lifecycle assessment process for large cryogenic storage tanks.
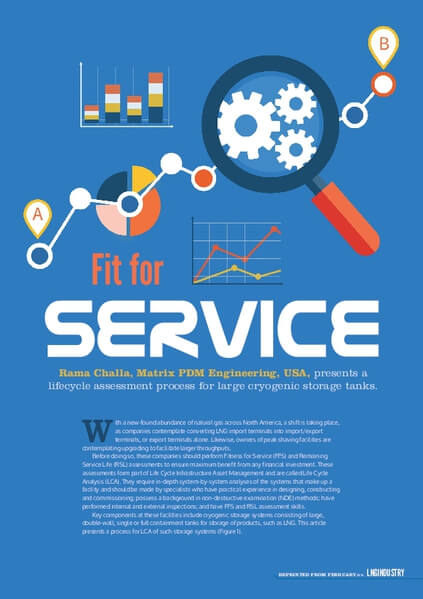
With a new-found abundance of natural gas across North America, a shift is taking place, as companies contemplate converting LNG import terminals into import/export terminals, or export terminals alone. Likewise, owners of peak shaving facilities are contemplating upgrading to facilitate larger throughputs.
Before doing so, these companies should perform Fitness for Service (FFS) and Remaining Service Life (RSL) assessments to ensure maximum benefit from any financial investment. These assessments form part of Life Cycle Infrastructure Asset Management and are called Life Cycle Analysis (LCA). They require in-depth system-by-system analyses of the systems that make up a facility and should be made by specialists who have practical experience in designing, constructing and commissioning; possess a background in non-destructive examination (NDE) methods; have performed internal and external inspections; and have FFS and RSL assessment skills.
Key components at these facilities include cryogenic storage systems consisting of large, double-wall, single or full containment tanks for storage of products, such as LNG. This article presents a process for LCA of such storage systems (Figure 1).
The first liquefied cryogenic petroleum gas storage facilities in the US were built around 1917. Technological evolutions over the last century have included the use of new materials, such as 9% Ni and 7% Ni steels, and single, double and full containment storage. Similarly, the regulatory environment has evolved with the adoption of National Fire Protection Association (NFPA) 59Al in 1967 and the first Federal LNG safety regulations in 1972. New developments include standards, such as API 6252 – a comprehensive standard from the American Petroleum Institute (API) for refrigerated storage tank systems; API 620 Appendices Q, R, for design and construction of cryogenic and refrigerated tanks; and ACI 3764 – a code from the American Concrete Institute (ACI) for construction of concrete refrigerated storage tanks.
Analysing the service life of these storage tanks requires a deliberative approach. Data must be clearly understood and procedures developed to ensure that obiectives are met. Additionally, good project management by the owner, engineer and contractor is critical.
While examples in this article are specific to LING, this process can also be applied to other systems used to store products, such as LPG, ammonia, liquid nitrogen, liquid oxygen and liquefied argon. Certain adjustments will be required based on specific construction details appropriate to the stored product.
The following three-phase execution strategy provides a structured approach.
Phase 1: data collection
Assessment begins with the collection of information, such as past tank loading and unloading cycles; design calculations; design and fabrication drawings; construction documentation (including material certificates, material test reports and weld procedures); and geotechnical reports, commissioning, operation, maintenance, repair and modification records. Certain facility operating information is also necessary, such as transport logs, which indicate loading/unloading information, temperature data, foundation settlement information, and historical tank vapour pressure information.
The operating history and anticipated past and future loading cycles form the basis for the FFS and RSL assessment (Figure 2).
Assumptions based on historic data of similar facilities and experience may be made if there are gaps in facility data or operating information.
Understanding the owner’s objectives forms a critical part of this phase, as this will significantly influence the work required in phases 2 and 3. A longer life expectancy, for example, will require closer evaluation and potentially more repairs. Similarly, if phase 2 analysis results in a long future life, the work in phase 3 can be minimised.
Phase 2: desktop study
The desktop study involves: data review and integration; design review; tank stress and fatigue analyses; identification of critical inspection areas to validate assumptions or findings; development of procedures to enable future on-site tank entry; inspection; repair and closure; and planning and scheduling activities.
Typical assessments are iterative, with various methods applied. Although the assessments focus primarily on the highly stressed, fatigue sensitive components of the liquid containing inner tank, they also cover aspects such as the foundation, insulation, penetrations, and platforms.
Critical components of the inner tank include: the circumferential weld of the shell to the annular plate; shell penetrations; local shell stiffeners; a portion of the shell at the stiffener ring attachment; and a circumferential lap weld of the bottom plate to the annular plate. Underpinning the assessment are.
- Finite Element Analyses (FEA) to identify regions that are susceptible to fatigue and to generate stresses and stress ranges.
- Fatigue analyses using crack growth models and damage accumulation mechanisms to estimate consumed design life and life available to sustain future demand.
The spectrum of topics covered is vast, and a complete depiction of the entire analyses is impractical. Therefore, only a few items are presented here (Figures 3 and 4).
A key issue in FEA modeling is the need to correctly mimic the as-built conditions to accurately depict peak stresses. Weld detail of a shell to annular plate joint is illustrated in Figure 5. Due to this process, the chimes typically curl up due to shrinkage.
A comparison of stresses on the inside toe of the shell to the annular plate joint (identified as a highly stressed, fatigue sensitive component) between a perfectly modeled condition and the curled up as-built condition of the annular plate chime, indicates peak stress variation as high as 50% from one to the other (Figure 6).
Another issue is geometric Stress Concentration Factors (SCFs). Occasionally, the FEA model and mesh size is not adequate to model the peak stresses. In such cases, SCFs can be utilised to properly depict the values. The SCs are based on published literature and experience of the analyst. One example of SCFs can be found in stress analysis and fatigue of welded structures.5
Fatigue is the driving mechanism in an LCA evaluation, as tanks are continually loaded and unloaded. Due to repeated or fluctuating stresses, pre-existing minute cracks in material grow. A fatique sensitive component will fail when these cracks propagate to a level that cannot be sustained (Figure 7).
Two approaches can be used for fatigue. The first is an S-N Curve approach®, where there is a finite number of cycles at a stress range at which a component fails. These curves exist for both smooth bar specimens and welded joints. For every joint under consideration:
- Stress ranges are determined using loads in a load cycle.
- The number of cycles at a joint for each load/unload cycle are identified using the loading regime.
- For every stress range associated with a load cycle, the number of cycles to failure is determined from published S-N Curves (Figure 8).
The ratio of cycles in the second and third items yields a damage fraction for a load cycle. Using a cumulative damage rule, such as the Miner’s rule”, one can determine the life of the joint under consideration. The cumulative damage fraction has two parts – life consumed and life remaining. Once all of the components have been evaluated, the minimum life remaining will yield the RSL.
Similar to an SCF, the surface profile of the welds used in construction amplifies the impact of fatigue (Figure 9). The impact is handled by using Fatigue Strength Reduction Factors (FSRF), which are selected by the analyst based on experience and as published in codes and standards.
In general, the S-N Curve approach yields an idea of the RSL of the components that make up the cryogenic storage tank. However, it does not provide any information on intermediate stages of propagation of a crack, due to the loading/unloading cycles.
A second approach is a Fracture Mechanics (FM) evaluation. This method has been validated in multiple industries. The premise for an FM evaluation is the growth of a postulated flaw at a location under cyclic loading. For analyses, a flaw at a specific location can be characterised based on the detectability per the acceptance criteria identified in the NDE used, or conservatively based on a design standard. Considering a postulated crack and using an acceptable material crack growth model, such as the modified Paris Law, one can simulate crack growth with every load cycle. The process can be summarised using a Failure Assessment Diagram (FAD).” Failure is considered when the crack becomes unstable per the FAD (Figure 10). This method can be used to gain additional insight into RSL.
Phase 3: entry, inspection, reassessment and repairs
Once the assessment has been completed, inspection requirements and potential upgrades are defined with emphasis on components with limiting fatigue value. Inspection requirements are developed using experience, industry norms, and API inspection standards. The main consideration for upgrades is the increase in design life.
During phase 3, the emphasis is on: identifying areas of concern; determining areas to be inspected; confirming and checking critical areas identified in the desktop study; revisiting the desktop study if required; performing upgrades; and returning the tank system to facility operations. Inspection data validates the engineering analyses assumptions, or may require them to be modified. Information from final analyses, coupled with inspection data, facilitates the development of repairs and upgrades to meet future facility requirements.
The first step in Phase 3 consists of purging and safe isolation of the tank before entry. Subsequent tasks include: removal of perlite from the suspended deck; installation of guillotine plates and perlite remover ports to remove perlite from interstitial areas; cutting of the door sheet area to facilitate movement of men and equipment; removal of the balance of perlite if required; and inspection of critical components. Repairs performed may include: joining the intermittent welds to create a continuous weld on the stiffener to shell connection; adding an additional weld to the annular to the bottom plate weld; and removing and replacing pumps, pump columns and pump column braces. In addition, all insulation removed for repair and entry purposes is replaced. Before the tank returns to service, the tank and associated piping is purged with nitrogen and then cooled down. All work performed during this phase must be performed using specifications, procedures and drawings developed during the previous phase.
Summary
While assessment methodologies are similar for different tank systems, each tank has its own characteristics and requires a facility specific process. The complexity requires that all phases of an LCA be carefully planned and flawlessly executed. It requires multiple skill sets and expertise in project management, stress analysis, tank design, welding engineering, fatigue and fracture mechanics, and construction.
The complexities demand focused management of the scope, deliverables and personnel by all parties to ensure that objectives are met without compromising cost, schedule and quality. Owners and contractors must ensure that their value interests are in alignment and that conflicts are minimised.
View the article as a PDF here.
References
- NFPA® 59A Standard for the Production, Storage, and Handling of Liquefied Natural Gas (LING), 2013 Edition, NFPA, 1 Batterymarch Park, Quincy, MA 02169-7471
- API 625, Tank Systems for Refrigerated Liquefied Gas Storage, 1* edition, August 2010 with Addendums 1, 2, November 2014, API, Washington, DC.
- API 620, Design and Construction of Large, Welded, Low-pressure Storage Tanks. API STANDARD 620\12th edition, October 2013, with Addendum 1. November 2014,
Washington, DC. - ACI 376-11 Code Requirements for Design and Construction of Concrete Structures for the Containment of Refrigerated Liquefied Gases and Commentary, An ACI Standard, May 2013, ACI, Farmington Hills, MI
- CHATTOPADHYAY, A., GLINKA, G, EI-ZEIN, M., QIAN, J, and FORMAS, R., Stress Analysis and Fatigue of Welded Structures,’ Welding in the World, July 2011, Vol. 55, Issue 7, pp. 2 – 21.
- 2013 ASME Boiler and Pressure Vessel Code, Section VIII Division 2, Rules for Construction of Pressure Vessels, Part 5.5, American Society of Mechanical Engineers (ASME), July 2013, NY, NY, p. 543.
- DIETER, G. E., Mechanical Metallurgy. SI Metric ed. N.p.: McGraw Hill, 1988, Print. III. p. 414.
- PIB-1-2014, ASME Boiler and Pressure Vessel Code, Section VIII, Division 2 Criteria and Commentary, American Society of Mechanical Engineers (ASME), May 2014, NY, NY, Figures 5 – 11, p. 208.
- 2013 ASME Boiler and Pressure Vessel Code, Section VIII Division 2, Rules for Construction of Pressure Vessels, Sec. 3.11.2.8 (c), American Society of Mechanical Engineers (ASME), July 2013, NY, NY, p. 72.
- HERTZBERG, R. W., Deformation and Fracture Mechanics of Engineering Materials. 4th edition, 1996, N.p.: Wiley, n.d. pp. 591 – 598. Print.
- API 579, Fitness For Service, Section 2.4.2.3, p. 2-8, and Figure 2.2, p. 2-16, API 579-1/ ASME FFS-1, 5 June 2007 (API 579 Second Edition), API, Washington, DC.